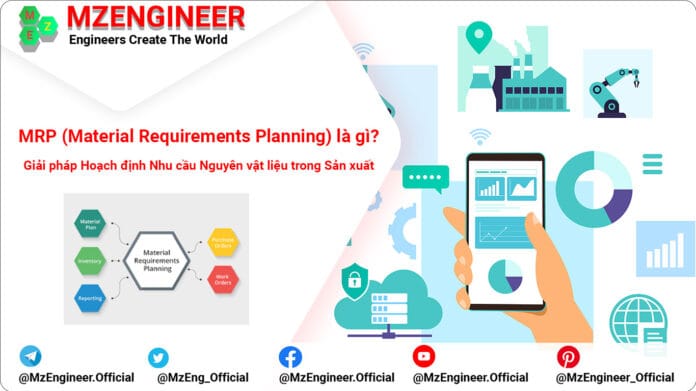
MRP (Material Requirements Planning) là gì? MRP, hay Hoạch định Nhu cầu Nguyên vật liệu, là hệ thống giúp doanh nghiệp lập kế hoạch và quản lý nguyên vật liệu hiệu quả trong sản xuất. Với MRP, doanh nghiệp có thể giảm chi phí tồn kho, đảm bảo nguyên vật liệu luôn sẵn sàng, và tối ưu hóa quy trình sản xuất. Cùng tìm hiểu các lợi ích, quy trình vận hành và sự khác biệt giữa MRP và ERP trong bài viết này.
MRP là gì? Tầm quan trọng của MRP
MRP là một hệ thống quản lý chuyên biệt, được thiết kế để tính toán và lập kế hoạch lượng nguyên vật liệu cần thiết cho quá trình sản xuất. Xuất phát từ nhu cầu giải quyết vấn đề tồn kho và đảm bảo đủ nguyên vật liệu cho sản xuất, MRP giúp doanh nghiệp tránh tình trạng thiếu hụt hoặc dư thừa tồn kho. Được phát triển từ những năm 1960, hệ thống MRP đã trở thành nền tảng trong quản lý sản xuất và là cơ sở cho các hệ thống hoạch định nguồn lực hiện đại như ERP (Enterprise Resource Planning).
MRP không chỉ là công cụ hỗ trợ quản lý nguyên vật liệu mà còn giúp doanh nghiệp tối ưu hóa quy trình sản xuất, giảm thiểu chi phí và cải thiện chất lượng sản phẩm.
Các thành phần chính của hệ thống MRP
Hệ thống MRP được xây dựng trên ba thành phần chính giúp doanh nghiệp lập kế hoạch, điều phối và kiểm soát nguồn nguyên vật liệu một cách hiệu quả:
- Dự báo nhu cầu sản phẩm: Dựa trên đơn đặt hàng từ khách hàng hoặc dự báo sản xuất, hệ thống MRP xác định số lượng sản phẩm cần sản xuất trong một khoảng thời gian nhất định. Điều này giúp doanh nghiệp có thể điều chỉnh kế hoạch sản xuất phù hợp với nhu cầu thực tế.
- Danh mục vật liệu (Bill of Materials – BOM): BOM là danh sách chi tiết các nguyên vật liệu, linh kiện cần thiết để sản xuất một sản phẩm. Hệ thống MRP dựa vào BOM để xác định chính xác số lượng từng loại nguyên vật liệu cần có trong kho.
- Kiểm soát tồn kho: Hệ thống MRP giúp theo dõi và quản lý tồn kho, nhằm đảm bảo rằng nguyên vật liệu luôn có sẵn khi cần thiết nhưng không vượt quá mức cần thiết để tránh lãng phí và chi phí lưu trữ cao.
Các bước vận hành của hệ thống MRP
Một hệ thống MRP thường bao gồm các bước sau để đảm bảo hiệu quả quản lý nguyên vật liệu:
- Xác định nhu cầu sản xuất: Dựa trên dự báo và đơn hàng, doanh nghiệp xác định nhu cầu sản xuất cho từng loại sản phẩm.
- Lập kế hoạch nguyên vật liệu: Hệ thống MRP phân tích BOM để xác định số lượng và loại nguyên vật liệu cần sử dụng, cũng như thời điểm cần đặt hàng hoặc sản xuất thêm.
- Xác định thời gian đặt hàng và sản xuất: Hệ thống tính toán thời gian sản xuất và giao hàng để đảm bảo nguyên vật liệu có mặt đúng lúc. Điều này giúp tối ưu hóa thời gian sản xuất và giảm thiểu lãng phí.
- Giám sát tồn kho và điều chỉnh kế hoạch: MRP giúp doanh nghiệp kiểm soát tình trạng tồn kho và điều chỉnh kế hoạch khi có sự thay đổi về nhu cầu hoặc tình trạng hàng hóa.
Lợi ích của MRP trong quản lý sản xuất
- Giảm tồn kho và chi phí lưu trữ: Hệ thống MRP giúp tối ưu hóa lượng tồn kho, tránh tình trạng dư thừa và giảm chi phí lưu trữ. Việc duy trì mức tồn kho hợp lý giúp doanh nghiệp tiết kiệm chi phí và tránh lãng phí.
- Đảm bảo nguyên vật liệu luôn sẵn sàng: MRP giúp đảm bảo nguồn cung nguyên vật liệu luôn sẵn sàng cho sản xuất mà không bị gián đoạn, giúp duy trì sự liên tục trong quy trình sản xuất.
- Tăng hiệu quả sản xuất: Bằng cách lập kế hoạch chính xác và dự báo tốt, hệ thống MRP giúp doanh nghiệp sử dụng nguyên vật liệu hiệu quả, tránh lãng phí và tối ưu hóa năng suất.
- Nâng cao khả năng ra quyết định: Với các báo cáo và phân tích từ MRP, nhà quản lý có thể ra quyết định kịp thời và chính xác, giúp cải thiện hiệu quả sản xuất.
- Cải thiện mối quan hệ với khách hàng: MRP giúp đảm bảo sản phẩm được giao đúng hạn, giảm thời gian chờ đợi của khách hàng và nâng cao sự hài lòng của khách hàng.
Các loại hệ thống MRP hiện nay
- MRP I: Đây là hệ thống MRP truyền thống, tập trung vào lập kế hoạch nguyên vật liệu và quản lý sản xuất. MRP I được xây dựng chủ yếu để giải quyết các vấn đề tồn kho và đảm bảo nguyên vật liệu cho sản xuất.
- MRP II (Manufacturing Resource Planning): Là phiên bản mở rộng của MRP I, hệ thống này không chỉ quản lý nguyên vật liệu mà còn tích hợp thêm các chức năng liên quan đến sản xuất, bao gồm lập kế hoạch sản xuất, quản lý năng lực và dự báo tài chính.
- ERP với phân hệ MRP: Đây là hệ thống ERP tích hợp các chức năng của MRP. Phân hệ MRP trong ERP giúp doanh nghiệp quản lý nguyên vật liệu và sản xuất đồng thời tích hợp với các bộ phận khác như tài chính, nhân sự và chuỗi cung ứng.
Các phần mềm MRP phổ biến
- SAP MRP: SAP là một trong những hệ thống ERP hàng đầu có tích hợp MRP, giúp doanh nghiệp vừa và lớn quản lý sản xuất hiệu quả.
- Oracle MRP: Hệ thống MRP của Oracle cung cấp khả năng lập kế hoạch chính xác và phù hợp với nhiều loại hình doanh nghiệp.
- Microsoft Dynamics 365: Microsoft Dynamics tích hợp MRP và ERP, giúp doanh nghiệp quản lý sản xuất và các hoạt động khác một cách hiệu quả.
- Odoo: Là hệ thống ERP mã nguồn mở với các tính năng MRP mạnh mẽ, Odoo phù hợp với doanh nghiệp nhỏ và startup.
- Infor MRP: Infor cung cấp giải pháp MRP linh hoạt, phù hợp cho các doanh nghiệp sản xuất có nhu cầu đặc thù.
Kết luận
MRP là công cụ không thể thiếu trong quản lý sản xuất, giúp doanh nghiệp lập kế hoạch nguyên vật liệu chính xác và đảm bảo sự liên tục trong sản xuất. Với khả năng tối ưu hóa tồn kho, giảm chi phí và nâng cao hiệu quả, MRP là nền tảng quan trọng giúp doanh nghiệp sản xuất duy trì và cải thiện năng lực cạnh tranh. Trong bối cảnh công nghệ phát triển, MRP kết hợp với ERP sẽ ngày càng được ứng dụng rộng rãi, giúp doanh nghiệp không chỉ tối ưu hóa hoạt động mà còn đạt được sự linh hoạt và hiệu quả tối ưu trong sản xuất.